- Client:
- Revert Group
- Location:
- Melbourne VIC
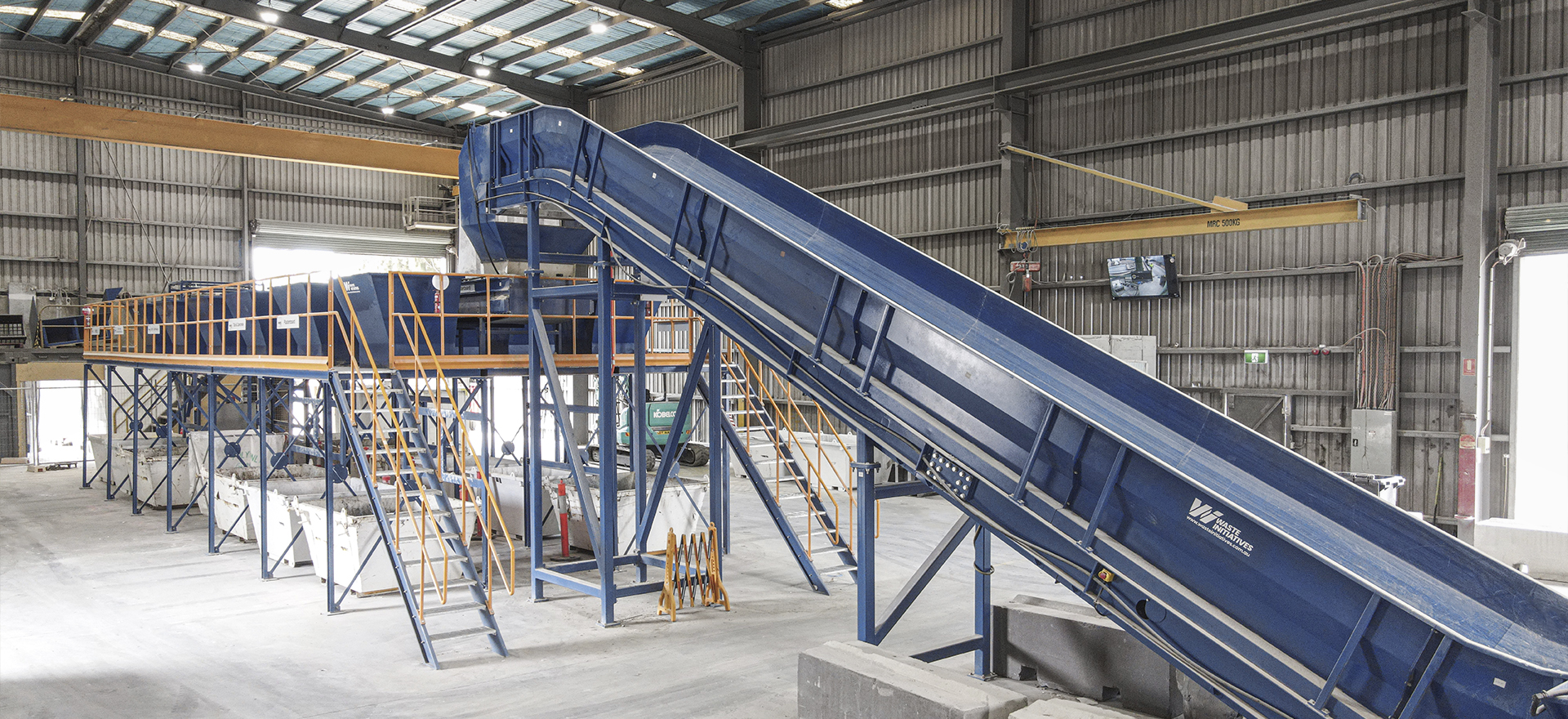
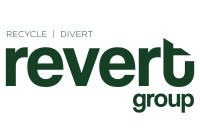
The Waste Initiatives installation team was fantastic, ensuring that they mobilised the site efficiently and safely.

Problem: Inadequate segregation of C&I/C&D waste
Revert Group, a company specialising in the fit-out and refurbishment sector of commercial and industrial waste (C&I), faced a critical challenge in efficiently managing their waste streams at their facility in Brooklyn, Victoria. With a diverse range of materials generated from their operations, including construction and demolition (C&D) waste, they struggled to segregate and recycle these materials effectively. The lack of a sophisticated sorting system led to inefficiencies in their operations and resulted in a significant portion of waste being sent to landfill, contrary to their sustainability goals.
Solution: Installation of a commercial and industrial waste sorting line
Waste Initiatives addressed Revert Group’s challenges by installing a customised C&I/C&D sorting line, enabling the segregation of 16 types of waste materials. This tailored solution facilitated Revert Group’s goal of recycling 90% of its waste, significantly reducing its environmental impact and waste disposal costs.
Paul Rosenberg Vella, Director and Co-Founder of Revert Group, praised Waste Initiatives’ hands-on approach, particularly for focusing on safety and dust mitigation. Regular design meetings ensured effective communication and alignment with Revert Group’s recovery objectives. Additionally, Paul appreciated Waste Initiatives’ proactive attitude and commitment to safety during site mobilisation and project execution, which minimised operational risks.
In conclusion, the collaboration between Revert Group and Waste Initiatives exemplifies the successful integration of innovative waste management solutions to address complex challenges in the construction and refurbishment sector, ultimately leading to enhanced efficiency and sustainability in operations.
Make An Enquiry
Talk to Waste Initiatives today to find out more about our waste & recycling solutions.




- Client:
- Volkswagen Group Australia
- Location:
- Chullora NSW & Derrimut VIC
Since installation, the unit has proven reliable, safe & user-friendly and is consistently achieving high bin payloads across both timber and cardboard waste streams. Our experience with the team at Waste Initiatives and their product has been completely satisfactory, and we have no hesitation in recommending them – great work guys.
Challenge
Introduced to Volkswagen by Remondis Australia, Waste Initiatives were engaged to assess a deteriorating compaction system at VW’s parts distribution centre at Chullora.
During Waste Initiatives’ site assessment, it became apparent that the range of cardboard box sizes/thicknesses and the timber crates/ pallets being disposed of were proving unmanageable and increasingly costly with the existing compactor.
Space being at a premium, the resulting waste overflow due to the inferior compaction performance of their old machine left the site with an ongoing logistics and material handling challenge which required excessive labour and increased collection services – inflating the site operating costs.
Solution
The ideal solution for Volkswagen was quickly indentified as the mutli-use RPV7700 Roll Packer fitted out with a special-purpose roller to ensure efficient compaction across both timber and cardboard waste streams, without cross- contaminating the bins.
An additional RP7700 Roll Packer was specified for VW’s sister DC in Melbourne.
Upon installation, the site immediately proved the benefit of the original Roll Packer – seeing a significant increase in bin payloads, effective crushing of the most challenging of their waste profiles (including over size crates & boxes), and a safe & reliable operating process delivering substantial savings on their operating costs and freeing up their labour resources.
Make An Enquiry
Talk to Waste Initiatives today to find out more about our waste & recycling solutions.

